钣金加工相关工艺-压铸工艺知识的详细介绍-中山哈尔滨敬轩运动鞋类有限公司
压铸是一种制造工艺,可以通过使用称为模具的可重复使用的模具生产几何形状复杂的金属零件。压铸工艺涉及使用熔炉,金属,压铸机和模具。金属,通常是诸如铝或锌的非铁合金,在炉中熔化,然后注入压铸机中的模具中。有两种主要类型的压铸机 - 热室机(用于低熔点合金,如锌)和冷室机(用于高熔点合金,如铝)。这些机器之间的差异将在设备和工具部分详细说明。但是,在这两台机器上 在将熔融金属注入模具后,它迅速冷却并凝固成最终部件,称为铸件。下一节将更详细地介绍此过程中的步骤。
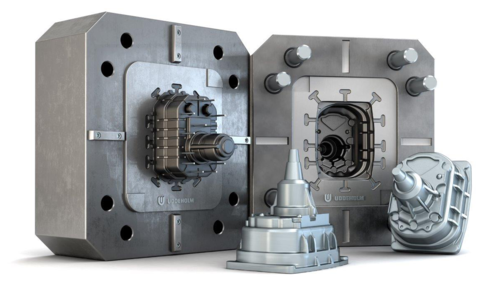
压铸热室机概述
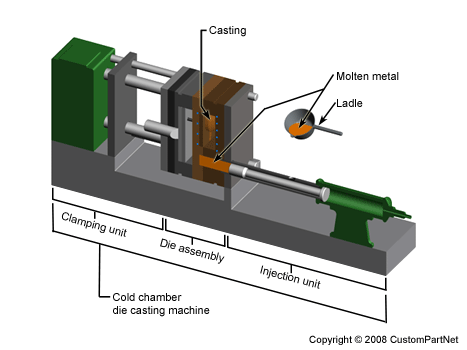
压铸冷室机概述
在这个过程中产生的铸件在尺寸和重量上可以变化很大,从几盎司到100磅不等。压铸件的一个常见应用是外壳 - 薄壁外壳,内部通常需要许多肋 和凸台 。用于各种器具和设备的金属外壳通常是压铸的。几种汽车部件也使用压铸件制造,包括活塞,汽缸盖和发动机缸体。其他常见的压铸件包括螺旋桨,齿轮,衬套,泵和阀门。
功能
名称 | 典型 | 可行 |
形状: | 薄壁:复杂 固体:圆柱形 固体:立方体 固体:复杂 | 扁平 薄壁:圆柱 薄壁:立方体 |
---|---|---|
零件尺寸: | 重量:0.5盎司 - 500磅 | |
材料: | 金属 铝 铅 镁 锡 锌 | 铜 |
表面处理 - Ra: | 32 - 63μin | 16 - 125μin |
宽容: | ±0.015英寸 | ±0.0005英寸 |
最大壁厚: | 0.05 - 0.5 in。 | 0.015 - 1.5英寸 |
数量: | 10000 - 1000000 | 1000 - 1000000 |
交货时间: | 月 | 周 |
好处: | 可生产大型零件 可形成复杂形状 高强度零件 非常好的表面光洁度和精度 高生产率低 劳动力成本 废料可以回收利用 | |
缺点: | 需要修整 高工具和设备成本 有限的模具寿命 长的交付周期 | |
应用: | 发动机部件,泵部件,设备外壳 |
与之比较:
免责声明:所有流程规范均反映流程功能的大致范围,仅供参考。实际能力取决于制造商,设备,材料和零件要求。
流程周期
压铸的工艺循环包括五个主要阶段,下面将对其进行说明。总 循环时间非常短,通常在2秒到1分钟之间。
1.
夹紧
2. - 第一步是准备和夹紧模具的两半。首先从先前的注射中清除每个半模,然后润滑以便于下一部分的弹出。润滑时间随着零件尺寸以及型腔和 侧芯的数量而增加。此外,在每个循环后可能不需要润滑,但在2或3个循环后,取决于材料。在润滑之后,连接在压铸机内部的两个半模被封闭并牢固地夹在一起。必须对模具施加足够的力以在注入金属时使其牢固地闭合。关闭和夹紧模具所需的时间取决于机器 - 较大的机器(具有较大夹紧力的机器)将需要更多时间。这个时间可以从机器的干循环时间估算。
3.
注射
4. - 将保持在炉中设定温度的熔融金属接着转移到腔室中,在腔室中将其注入模具中。转移熔融金属的方法取决于压铸机的类型,无论是使用热室还是冷室机。该设备的不同之处将在下一节中详述。一旦转移,熔融金属在高压下注入模头。典型的注射压力范围为1,000至20,000 psi。该压力在凝固期间将熔融金属保持在模具中。注入模具中的金属量称为注射。注入时间是熔融金属填充模具中所有通道和空腔所需的时间。该时间非常短,通常小于0.1秒,以防止任何一部分金属的早期固化。适当的注入时间可以通过材料的热力学性质以及铸件的壁厚来确定。壁厚越大,注入时间越长。在使用冷室压铸机的情况下,注入时间还必须包括手动将熔融金属浇注到注射室中的时间。
5.
冷却
6. - 注入模具中的熔融金属一旦进入模腔就会开始冷却并凝固。当填充整个空腔并且熔融金属凝固时,形成铸件的最终形状。在冷却时间结束并且铸件凝固之前,模具不能打开。冷却时间可以从金属的几种热力学性质,铸件的最大壁厚和模具的复杂性来估算 。壁厚越大,冷却时间越长。模具的几何复杂性还需要更长的冷却时间,因为额外的热阻力。
7.
喷出
8. - 在预定的冷却时间过去之后,可以打开半模,并且弹出机构可以将铸件推出模腔。打开模具的时间可以从机器的干燥循环时间估算,喷射时间由铸件外壳的尺寸确定, 并且应该包括铸件从模具中脱落的时间。弹出机构必须施加一些力才能弹出零件,因为在冷却过程中零件会收缩并粘附在模具上。一旦铸件被弹出,就可以夹紧模具以进行下一次注射。
9.
修剪
10. - 在冷却过程中,模具通道中的材料将凝固附着在铸件上。这种多余的材料以及 已发生的任何闪光必须通过切割或锯切手动或使用修边压力机从铸件上进行修整。修剪多余材料所需的时间可以从铸件外壳的尺寸估算。由此修整产生的废料要么被丢弃,要么可以在压铸过程中重复使用。在将再循环材料与非再生金属结合并在压铸工艺中重复使用之前,可能需要将再生材料修复为适当的化学成分。
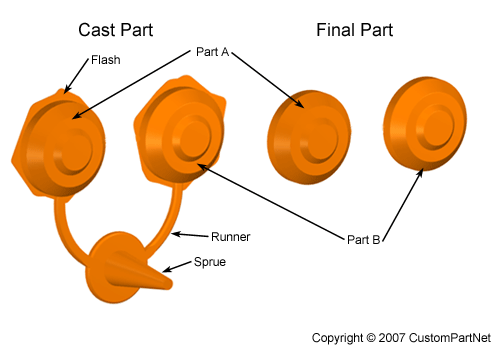
压铸件
设备
两种类型的压铸机是热室机和冷室机。
·
热室压铸机
· - 热室机器用于低熔点合金,如锌,锡和铅。熔化其他合金所需的温度会损坏泵,泵与熔融金属直接接触。将金属装在一个敞开的保温罐中,将其放入炉中,在那里将其熔化到所需的温度。然后熔融金属流入喷丸腔室通过入口和柱塞,由液压驱动,迫使熔融金属通过鹅颈通道进入模具。热室压铸机的典型注射压力为1000至5000psi。在将熔融金属注入模腔后,柱塞保持向下,在铸件凝固时保持压力。凝固后,液压系统缩回柱塞,部件可由夹紧单元弹出。在注入熔融金属之前,该单元关闭并夹紧模具的两半。当模具连接到压铸机时,每一半都固定在称为压板的大板上 。模具的前半部分称为盖模,安装在固定压板上并与鹅颈管道对齐。模具的后半部分(称为顶出模具)安装在可移动的压板上,该压板沿着拉杆滑动。液压动力夹紧单元致动夹紧杆,该夹紧杆将该压板推向盖模并施加足够的压力以在注入熔融金属时保持其闭合。在模腔内部金属凝固之后,夹紧单元释放半模并同时使喷射系统将铸件推出开口腔。然后可以关闭模具以进行下一次注射。
热室压铸机 - 开启
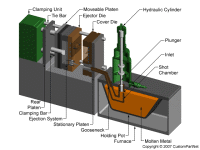
热室压铸机 - 关闭
·
冷室压铸机
· - 冷室机器用于熔化温度高的合金,不能在热室机器中铸造,因为它们会损坏泵系统。这种合金包括铝,黄铜和镁。熔融金属仍然装在一个敞开的保温罐中,该保温罐放入炉中,在那里熔化到所需的温度。然而,该保持罐与压铸机分开,并且每次铸造时熔融金属从罐中舀出,而不是被泵送。通过浇注孔将金属从浇包倒入注射室。冷室机器中的注射系统的功能类似于热室机器的注射系统,但它通常水平定向,不包括鹅颈通道。由液压驱动的柱塞迫使熔融金属通过喷射室并进入模具中的喷射套筒。冷室压铸机的典型注射压力为2000至20000psi。在将熔融金属注入模腔后,柱塞保持向前,在铸件凝固时保持压力。凝固后,液压系统缩回柱塞,部件可由夹紧单元弹出。夹紧单元和模具的安装与热室机器相同。有关详细信息,请参阅上一段。
冷室压铸机 - 开启
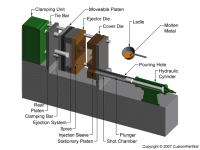
冷室压铸机 - 封闭式
机器规格
热室和冷室压铸机的典型特征在于它们提供的夹紧力的吨位 。所需的夹紧力由 模具中零件的 投影面积和注入熔融金属的压力决定。因此,较大的部件将需要较大的夹紧力。而且,某些需要高注射压力的材料可能需要更高吨位的机器。零件的尺寸还必须符合其他机器规格,例如最大 喷射量, 夹紧行程,最小模具厚度和压板 尺寸。
压铸件的尺寸可以变化很大,因此要求这些措施覆盖非常大的范围。结果,压铸机被设计成各自适应这种更大范围的值的小范围。下面给出几种不同的热室和冷室压铸机的样品规格。
类型夹紧力(吨)最大。注射量(oz。)夹紧行程(英寸)闵。模具厚度(in。)压板尺寸(英寸)
类型 | 夹紧力(吨) | 最大。注射量(oz。) | 夹紧行程(英寸) | 闵。模具厚度(in。) | 压板尺寸(英寸) |
热室 | 100 | 74 | 11.8 | 5.9 | 25 x 24 |
热室 | 200 | 116 | 15.8 | 9.8 | 29 x 29 |
热室 | 400 | 254 | 21.7 | 11.8 | 38 x 38 |
冷室 | 100 | 35 | 11.8 | 5.9 | 23 x 23 |
冷室 | 400 | 166 | 21.7 | 11.8 | 38 x 38 |
冷室 | 800 | 395 | 30.0 | 15.8 | 55 x 55 |
冷室 | 1600 | 1058 | 39.4 | 19.7 | 74 x 79 |
冷室 | 2000 | 1517 | 51.2 | 25.6 | 83 x 83 |
工装
注入熔融金属的模具是在该过程中使用的定制工具。模具通常由两个半部组成 - 盖模,其安装在固定 压板上 ;以及喷射器模,其安装在可动压板上。这种设计允许模具沿其分型线打开和关闭 。一旦关闭,两个半模形成内部部分腔,其填充有熔融金属以形成铸件。该腔由两个插入件形成,腔插入件和芯插入件分别插入盖模和喷射器模中。盖模允许熔融金属从注射系统流过开口,并进入零件腔。喷射器模具包括支撑板和喷射器盒,喷射器盒安装在压板上并且内部包含喷射系统。当夹紧单元将半模分开时,夹紧杆将顶出板向前推入顶出盒内,顶出盒将顶出销推入模制部件中,将其从芯插入件中弹出。
模具渠道
熔融金属流入零件腔体需要多个通道,这些通道集成在模具中并且对于热室机器和冷室机器而言略有不同。在热室机器中,熔融金属通过称为浇口衬套(在盖模中)的部件进入模具并在浇口涂布器(在喷射器模头中)周围流动。浇口是指进入模头的熔融金属的主要通道。在冷室机器中,熔融金属通过注射套管进入。进入模具后,在任何一种类型的机器中,熔融金属流过一系列流道并通过浇口进入零件腔,指导流动。通常,空腔将包含称为溢流井的额外空间,其在凝固期间提供额外的熔融金属源。当铸件冷却时,熔融金属将收缩并且需要额外的材料。最后,包括从模腔到模具外部的小通道。这些通道用作通气孔,以允许空气逸出模腔。流过所有这些通道的熔融金属将凝固附着在铸件上,并且在喷射后必须与部件分离。一种不填充材料的通道是冷却通道。这些通道允许水或油流过模具,邻近空腔,并从模具中移除热量。
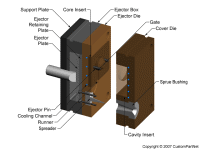
模具组装 - 开放式
(热室)
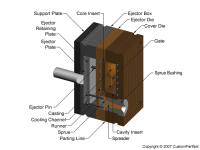
模具组装 - 封闭
(热室)
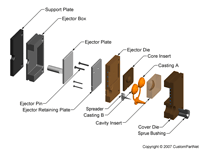
模具装配 - 爆炸视图
(热室)
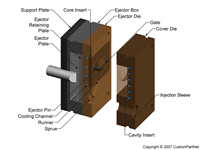
模具组装 - 开启
(冷室)
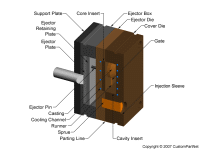
模具组装 - 封闭
(冷室)
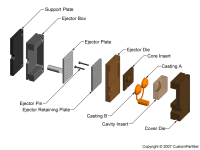
模具装配 - 爆炸视图
(冷室)
模具设计
除了这些多种类型的通道之外,在模具的设计中还必须考虑其他设计问题。首先,模具必须允许熔融金属容易地流入所有空腔。同样重要的是从模具中移除凝固的铸件,因此 必须在部件腔的壁上施加拔模角度。模具的设计还必须适应零件上的任何复杂特征,例如底切,这将需要额外的模具件。这些装置中的大多数通过模具的侧面滑入零件腔中,因此称为滑动或 侧向动作。最常见的侧面作用类型是侧芯,可以 模制外部底切。设计模具的另一个重要方面是选择材料。模具可以由许多不同类型的金属制成。高等级工具钢是最常见的,通常用于100-150,000次循环。然而,具有低碳含量的钢更耐开裂并且可以用于1,000,000次循环。其他常用的模具材料包括铬,钼,镍合金,钨和钒。在模具中使用的任何侧芯也可以由这些材料制成。
物料
压铸通常使用非铁合金。压铸的四种最常见的合金如下所示,以及它们的性质的简要描述。(按照链接搜索材料库)。
物料 | 属性 |
铝合金 |
|
铜合金 |
|
镁合金 |
|
锌合金 |
|
压铸材料的选择基于几个因素,包括密度,熔点,强度,耐腐蚀性和成本。材料也可能影响零件设计。例如,使用锌是一种高延展性金属,与许多其他合金相比,可以使壁更薄,表面光洁度更好。该材料不仅决定了最终铸件的性能,还影响了机器和工具。具有低熔融温度的材料,例如锌合金,可以在热室机器中压铸。然而,具有较高熔化温度的材料,例如铝和铜合金,需要使用冷室机器。熔化温度也影响工具,
可能的缺陷
缺陷 | 原因 |
闪 |
|
未填充的部分 |
|
泡泡 |
|
热撕裂 |
|
喷射器标记 |
|
许多上述缺陷是由不均匀的冷却速率引起的。冷却速率的变化可能由不均匀的壁厚或不均匀的模具温度引起。
设计规则
最大壁厚
· 减小零件的最大壁厚,以缩短循环时间(具体为喷射时间和冷却时间)并减小零件体积
不正确的 部分有厚厚的墙壁
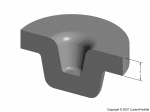
正确的 部分重新设计薄壁
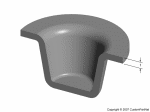
· 均匀的壁厚将确保均匀冷却并减少缺陷
不正确 的非均匀的壁厚(T 1 ≠吨2)

正确的 均匀壁厚(t 1 = t 2)
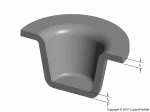
角落
· 圆角可减少应力集中和断裂
· 内半径应至少为壁的厚度
不正确的 角落
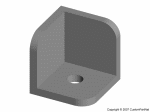
正确的
圆角
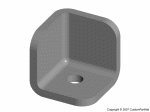
草案
· 在平行于分型方向的所有壁上施加拔模角度,以便于从模具中取出零件。
· 铝:墙壁为1°,内芯为2°
· 镁:墙壁为0.75°,内芯为1.5°
· 锌:墙壁为0.5°,内芯为1°
不正确 不拔模斜度
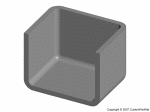
正确
拔模角度(q)
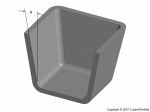
退刀槽
· 最大限度地减少外部底切的数量
· 外部底切需要侧芯,这会增加工具成本
· 通过重新定位分型线可以铸造一些简单的外部底切
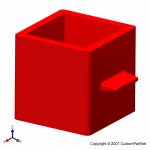
简单的外部底切
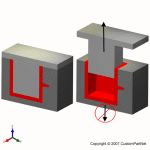
死不能分开
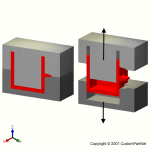
新的分型线允许底切
o 重新设计功能可以删除外部底切
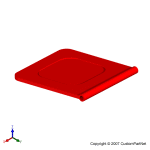
部分铰链
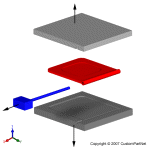
铰链需要侧芯
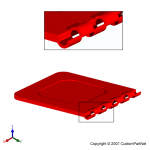
重新设计的铰链
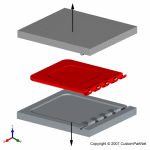
可以铸造新的铰链
· 移除所有需要 升降器的内部底切 - 这些设备的干扰通常发生在压铸中
· 在部件侧面设计开口可以允许侧芯形成内部底切
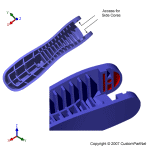
内侧 底切可从侧面进入
o 重新设计零件可以移除内部底切
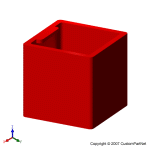
部分内部底切
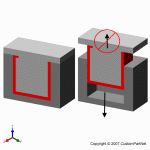
死不能分开
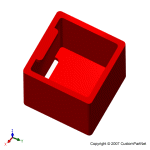
部分经过重新设计
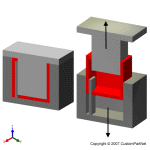
新部分可以投射
· 最小化副作用方向的数量
· 额外的侧向动作方向将限制模具中可能的腔体数量
生产成本
材料费用
材料成本取决于所需材料的重量和材料的单价。材料的重量显然是零件体积和材料密度的结果; 但是,该部件的最大壁厚也可以发挥作用。所需材料的重量包括填充模具通道的材料。壁较薄的部件需要较大的通道系统,以确保整个部件快速均匀地填充,因此将增加所需材料的数量。然而,这种附加材料通常小于部分体积减少所节省的材料量,这是由于壁较薄所致。因此,尽管通道较大,但使用较薄的壁通常会降低材料成本。
生产成本
生产成本主要根据小时费率和周期时间计算。每小时的速率与所使用的压铸机的尺寸成正比,因此了解零件设计如何影响机器选择非常重要。压铸机通常通过它们提供的夹紧力的吨位来表示。所需的夹紧力由投影面积决定注入熔融金属的部件和压力。因此,较大的部件将需要较大的夹紧力,因此需要更昂贵的机器。而且,某些需要高注射压力的材料可能需要更高吨位的机器。零件的尺寸还必须符合其他机器规格,例如夹具行程, 压板尺寸和注射量。除了机器的大小,机器的 类型 (热室与冷室)也会影响成本。使用具有高熔化温度的材料,例如铝,将需要通常更昂贵的冷室机器。
循环时间可以分解为注射时间,冷却时间和重置时间。通过减少这些时间,生产成本将降低。通过减小部件的最大壁厚可以减少注射时间。此外,某些材料可以比其他材料更快地注入,但注射时间非常短,节省的成本可以忽略不计。通过使用热室机器可以节省大量时间,因为在冷室机器中,熔融金属必须被舀入机器中。这个拉杆时间取决于击球重量。对于较低的壁厚,冷却时间也会减少,因为它们需要较少的时间来冷却。材料的几种热力学性质也影响冷却时间。最后,复位时间取决于机器尺寸和零件尺寸。较大的部件将需要来自机器的较大运动来打开,关闭和弹出部件,并且较大的机器需要更多时间来执行这些操作。另外,使用任何side-cores会减慢这个过程。
加工成本
模具成本有两个主要组成部分 - 模具和模腔加工 。模组的成本主要受零件外壳尺寸的控制。较大的部件需要更大,更昂贵的模组。加工型腔的成本几乎受到零件几何形状的每个方面的影响。主要成本驱动因素是必须加工的腔体尺寸,通过腔体的投影面积(等于部件和投影孔的投影面积 )及其深度来测量。任何其他需要额外加工时间的元素都会增加成本,包括特征数,分型面, 侧芯,公差和 表面粗糙度。
所使用的零件和材料的数量将影响 加工寿命,从而影响成本。具有高铸造温度的材料(例如铜)将导致较短的工具寿命。锌可以在较低温度下铸造,可以延长工具使用寿命。随着生产量的增加,这种效果变得更加成本过高。
最后一个考虑因素是副作用的数量方向,可间接影响成本。侧核的额外成本取决于使用的数量。然而,方向的数量可以限制可以包括在模具中的腔的数量。例如,用于需要3个侧芯方向的部件的模具只能包含2个腔。没有直接增加成本,但使用更多空腔可能会进一步节省成本。
推荐阅读:

相关文章
钣金加工机箱机柜时外观的尺寸是如何保持良好?
随着经济的发展,钣金机箱机柜以其诸多优点在我国得到越来越广泛的应用。对于钣金机箱机柜来说,它具有良好的外在形象,长期在户外工作对其影响很大。因此,机箱机柜钣金外壳的表面处理会给它带来很大的影响。机柜机...
钣金机箱加工模具成型和数控加工哪个成本低
钣金机箱中究竟是数控加工的成本低还是模具成型的成本低呢?如果有量,钣金厂基本上都是开模具的,开模具后,效率高,质量好,而且单价会下降很多。小批量和非标一般都是用数冲加工的,数冲一个小时200RMB以上...
材料课堂:不锈钢334的材质介绍
840(S33400)合金是一种含钛和铝的奥氏体不锈钢,含有足够的铬形成并维持足够规模的铬氧化物,使其在高温条件下得到保护,比传统铬镍不锈钢如304更耐高温;较高的含镍量,使其相比标准的18...
使用激光切割机精密度明显提升
以前国内各行业一般都选择手工裁切,劳动强度大,对操作者的技术要求也很高,如果有相贯线切割禁绝、坡口视点不均匀等原因,直接导致焊接质量达不到要求,激光切割机由于其加工工艺的特殊性,成为许多职业的选择。管...
铭偌教你如何让钣金机箱使用期限延长_铭偌钣金加工
不论什么样的机箱钣金加工暴露在空气中时刻长了,都会感染尘埃,或许有氧化表象,变得不再那么鲜亮,咱们是不是有办法能够应对钣金机箱的这种状况呢?或许说关于钣金机箱咱们大概怎么进行养护呢?关于钣金机箱进行养...
钣金加工型钢下料时需要注意这四点
(1)关于板厚的处理:一般情况下,板厚会影响切角尺寸和展开材料的长度。 角钢或槽钢向内弯曲时,展开长度以内皮为基准; 角钢或槽钢外弯时,其展开长度以外皮为准; 前者以倒角内皮为准,后者以外皮为准。 如...
精密钣金加工需要把控好哪些因素?
由操作者主导的过程造成的缺陷一般可以由操作者控制。造成操作失误的主要原因有:操作人员质量意识差、操作过程中粗心大意、不遵守操作规程、操作技能低、技术不熟练、因简单重复的工作而感到厌烦。相对而言,焊接过...
传统工艺与新钣金加工技术之间的区别
在我国,钣金加工在机械类中作用很大。钣金加工技术的飞速发展,使得板材加工技术水平不断提高。但是,钣金加工的工艺难点很大,影响到钣金加工技术推进的速度。看到了新的希望,激光加工的崛起让我们看到了新的希望...